Maintenance Advice to Keep Your Equipment Running Smoothly in Australia
Operation And Maintenance
To obtain the best performance from any attachment, it is imperative that it is correctly installed and that the carrier machine supplying the hydraulic power is also operating properly.
The checklist below will assist in the installation:
- Ensure the hydraulic circuit targeted for the attachment matches the requirements for hydraulic flow and pressure relief settings.
- Ensure the hydraulic piping and hose size matches the requirements of the attachment.
- The hydraulic oil and filter must be clean, and make sure the hydraulic reservoir is always full.
- Ensure that any hoses or tubes that are used are routed to prevent rubbing or chafing during operation.
Lubrication is the single most important procedure for sustaining the life of any attachment, and it is critical that the correct grease is applied to the equipment as per instructions in the individual manuals.
If you prefer, an automatic greasing system can also be fitted to save time and money, and, as always, please remember that regular servicing will eliminate excessive repair costs.
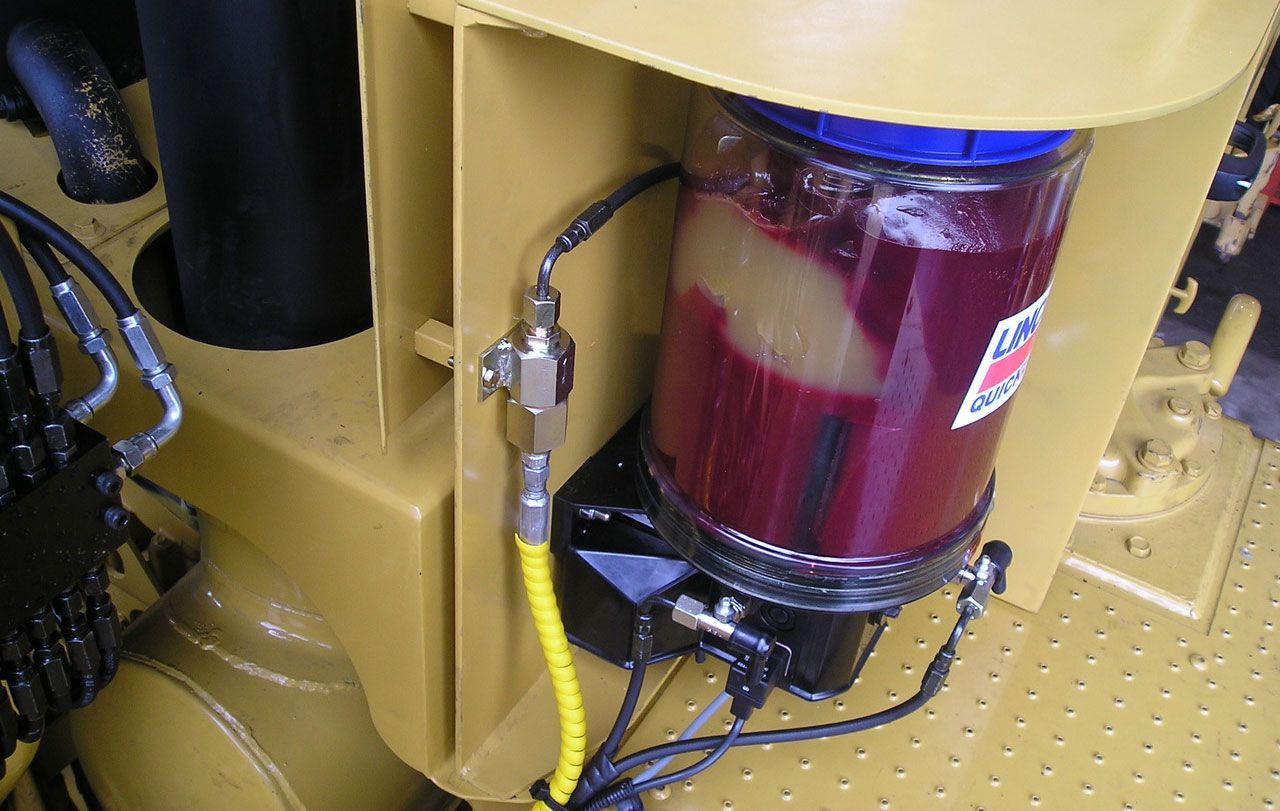
Crushing And Screening Buckets Operation
The total weight of the load (weight of bucket + weight of load material + any optional accessories) should not exceed the arm lifting capacity of the operating machine.
Most screening and crushing buckets require a case drain to be fitted to the host machine, and the MB Crusher Buckets have shims that can be inserted to reduce the size of the output material or removed to increase the size of the output material. The MB Crusher Bucket can be utilised with an iron magnet or dust suppression and may be installed on excavators, skid steers and loaders for one-man operation.
Easily be carried out by an operator, the screens on the MB Screening buckets come in various sizes, and the panels can be removed and replaced for a different size output. In the event of jamming, it is recommended to have the basket of the bucket turn in the opposite direction.
The Remu Screening buckets operate via various-sized screening and crushing rotors. The screening rotors separate the material whilst the crushing rotors break down hard lumps like glass, roof tiles, bitumen and clay. The Remu buckets may be used on excavators, skid steers and loaders.
Greasing should be carried out as per the manual instructions for the various components, and as always, it is important to remember that periodic service and repairs should be completed by our qualified hydraulic technicians.
Rockbreaker Operation
When operating a rockbreaker, please remember the following:
- Do not operate the breaker continuously in one spot for more than 20 seconds. Doing so will cause excessive heat that could mushroom the end of the tool.
- Always keep the tool 90° to the surface of the rock to reduce side loading on the tool bushings.
- Breaking along a rock’s natural faults and seams makes breaking easier. Start at the edge and work towards the centre.
- When breaking on a wall or steep incline, use a combination of the carrier’s stick cylinder and tilt cylinder to provide the necessary force to hold the breaker against the material. Always work the tool at 90° to the material being broken.
- As down-force is applied on the breaker, the carrier will lift slightly, indicating breaker tool is properly pressed onto the material.
- Do not use the breaker to pry, pick, pound, or lift, as this can cause serious damage. The tool must always move freely straight up and down in the bushing.
Avoid Blank Firing
Stop the movement of the breaker’s piston when full contact with the target material is lost. This reduces the strain on the tool retainers and front head during normal operation.
Blank firing emits a distinct metallic ringing sound and most often occurs in hard rock. With no contact material, the piston smashes the tool and retainers into the front head, thereby transferring the breaking force back through the breaker and excavator. This can cause premature failure of the parts in the lower end of the breaker.
To prevent blank firing, it is important to learn to anticipate when the material will break. Predicting this moment is probably best done by listening to the sound of the tool hitting the rock. A noticeable change in sound is noticed as the tool breaks through, and this is when to stop firing the breaker.
When not in use, the rockbreaker should be left standing vertically or lying at a 45° angle to eliminate sitting water and rusting of the inner components.
Keep your equipment running smoothly with our reliable maintenance services. Contact us now to discuss your maintenance needs.